Quality Simplified
Contrary to the traditional definition of quality, the Cost of Quality encompasses an organization’s entire production process developed to meet its product standard.
Defined by the American Society of Quality, the Cost of Quality is a methodology that enables producers to calculate how much of their resources are spent on activities preventing poor quality and is used to assess the quality of the organization’s goods and services and gauge the results of internal and external failures.
The
Cost of Quality (CoQ) is illustrated by the sum of two components - the
Cost of Good Quality (CoGQ) and the
Cost of Poor Quality (CoPQ).
Now, let’s define those components…
The
Cost of Good Quality (CoGQ) includes the total number of activities a business partakes in to ensure that its customers receive a product or service of the best possible quality.
Prevention costs are planned costs to ensure every process is in place. These include:
- Developing and implementing a Quality Management System (‘QMS’), quality planning, education, training, process capability, APQP/DFSS, FMEA, and FTA
Appraisal costs
are costs associated with determining the effectiveness of a QMS affecting both producers and the supply chain. These include:
- Calibrating, auditing, testing, verification, maintenance, market research, incoming inspection, in-process inspection, and final inspection
The
Cost of Poor Quality (CoPQ)
can occur during a company’s operations and even haunt you after products are shipped. The
hidden costs of poor quality (opportunity cost of lost sales, excess inventory, additional procedures, complaint investigations, damage to brand reputation, and increasing visits from regulators) are often much greater than the
visible costs that organizations track (rejection, repair cost, rework, and the cost of inspection).
To be clear, the hidden costs of poor quality will NOT show up on a P&L statement. These costs are embedded throughout the organization and typically represent anywhere between
20-35% of top-line revenues.
Internal failure costs are costs incurred when a company discovers quality failures prior to the delivery of items to customers. These include:
- Process delays, rework, scrap, retesting, CAPA/RCA, and capacity loss
External failure costs are the most substantial costs and are usually only evident after the products have been delivered. These include:
- Customer returns, loss of customer sales, low customer satisfaction, and brand distrust
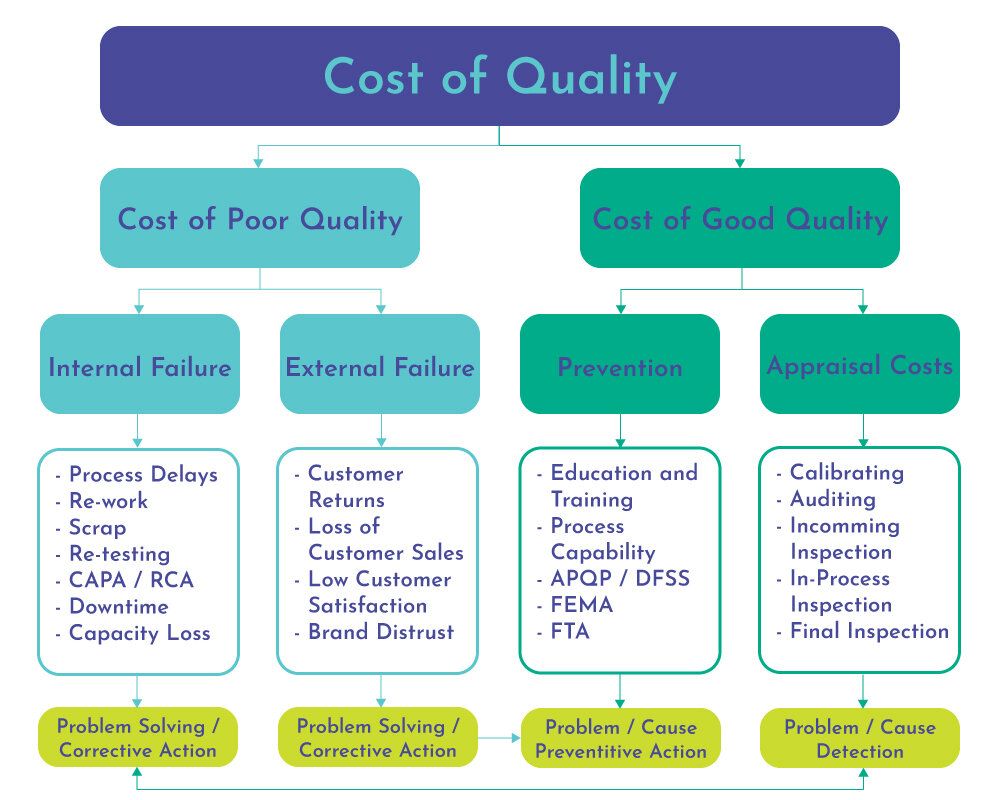
Enabling a ‘Culture of Quality’
With legalization creating one of the fastest-growing industries of our time, the emerging market has seen institutional voids. Designed to foster this growing market, a Quality Management System (QMS) ensures both emerging and established companies are in a better position to ensure quality, data integrity, and compliance.
Hear from Curaleaf’s VP of Quality Assurance in our latest press release.
Depending solely on compliance without considering the Cost of Quality may result in a few unexpected costs or significant waste - both having the potential to harm the bottom line and damage company reputation.
A cannabis company’s C-Suite tends to be ‘blind’ to the costs of both good and poor quality because many of them are tough to quantify. For example, damage to reputation via complaints and recalls or the cost of contaminated batches that do not end up getting released.
Nonetheless, these costs exist.
Managing Your Cost of Quality
Now, it’s time to manage. Identifying cost opportunities, things your company can do to improve its performance, and calculating an issue’s true expense can provide your business with the tactics and clarity you need to reduce the Cost of Quality.
With that said, improvements need to be a top priority on everybody’s list.
Enabling you to focus on core activities, business objectives, and KPIs that actually count, investing in a QMS deters additional time spent revising poorly developed products, dealing with customer dissatisfaction, and handling process delays.
C15 Solutions serves
60% of the top
10
publicly-traded cannabis companies (by market cap.) and acts as an internal partner to its customers through a team of dedicated Subject Matter Experts with a strategic focus on reducing the Cost of Quality.
C15’s three years of aggregated data demonstrate that customers obtain a return on investment (ROI) between 750-1,000% (not a typo!) with multi-state operators saving millions of dollars per year in quality and production costs. With customized subscription renewal case studies provided to each of our customers, we ensure they are getting the most out of our system.
Learn more about C15’s efficiencies.
Addressing your company’s total Cost of Quality may seem overwhelming or costly but we urge you to consider the following quote from Benjamin Franklin, “The bitterness of poor quality remains long after the sweetness of low price is forgotten.”